Cooling towers are integral parts of HVAC systems, vital in various industrial, commercial, and institutional settings that facilitate heat transfer and thermal management. However, continuous working of the cooling tower components and parts can lead to debris or dust buildup, growth of waterborne pathogens, and accumulation of mineral deposits. All these can hinder the overall performance and productivity of the cooling towers. So, regular maintenance and cleaning is very recommended for proper functioning.
This article will discuss a step-by-step guide on how to clean a cooling tower, its advantages, and precautions. This blog will cover the best practices, safety protocols, and expert recommendations.
Table of Contents (How to Clean a Cooling Tower)
Why You Should Clean Your Cooling Towers?
To keep cooling towers working efficiently, you should maintain their cleaning process regularly.
Proper maintenance and thorough cleaning of a cooling tower is crucial for regular cleaning, eliminating harmful impurities and debris that can harm its efficiency and pose health risks. Here are some vital advantages of a regular cooling tower:
Prevent clogging: Routinely cleaning the towers prevents debris, dirt, and biological growth from being obturate in different parts, such as spray nozzles, fill material, drains, and distribution systems. Regular cleaning also removes magnesium, calcium, and other minerals that continuously accumulate in the tower. By removing all this debris, you can enhance the overall performance and proper operation of the cooling towers.
Improve efficiency and performance: Cleaning ensures unrestricted airflow, water flow heat transfer rates, cooling capacity, and system reliability. All these lead to improved optimal efficiency and performance. This reduces energy consumption, lower operating costs, and extended equipment lifespan.
Enhances heat transfer: A regular cleaning process also improves the basic working of the towers, to cool the water by upgrading the heat transfer process. Once the blocking and obstructing materials are washed off and other necessary maintenance is done, it ultimately leads to better heat transfer between water and air.
Reduce the risk of diseases: As the fundamental work of these towers is to cool the water, it can also lead to the growth of waterborne pathogens, particularly Legionella, and encourage biofilm formation. Therefore, regular cleaning is vital to prevent such health risks and ensure a safe environment to work.
Cost savings: Disinfecting and washing the cooling towers regularly, reduces energy consumption by almost 20 % and lowers the maintenance and repair costs. You can also prevent corrosion and scaling by removing dirt and debris, improving lifespan and operational benefits.
Visual Inspection of Cooling Towers
The first step in the cleaning cooling tower process is its thorough visual inspection and analysis of the entire area. Complete visual inspection should be done at least a month to ensure maximum efficiency and troubleshoot early signs of damage.
The complete inspection of the cooling tower on the day of cleaning can reveal all the areas that need immediate action and repairs to prevent costly solutions such as cooling tower parts repairs or replacements. You have to focus on mainly:
- Any visible sign of damage, such as scaling, corrosion, or leakage.
- Fill media in case of any microbial mineral buildup or blockage.
- Sudden strange noises or vibrations from cooling tower motors, fans, gearboxes, or other equipment.
- Visible slush in the hot water basin.
- Clogging in the spray nozzles or the water distribution system.
After examining all these areas, inspect the drift eliminators and note the areas where extra maintenance and cleaning are required to boost the cooling capacity and run efficiently.
Protects Yourself From Harmful Chemicals
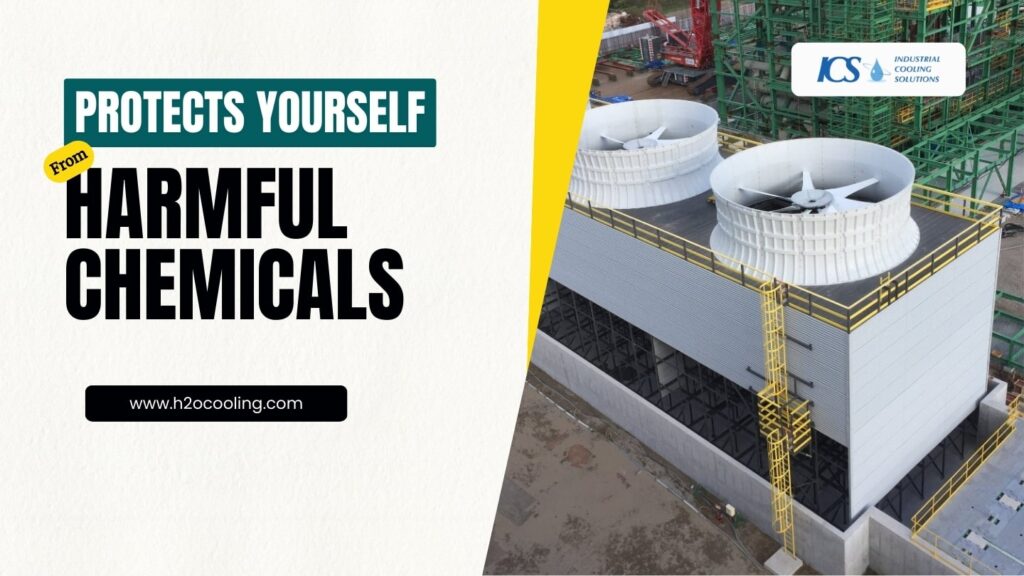
Self-protection comes first when dealing with harmful chemicals of microorganisms (microbial growth). While cleaning the cooling towers, there is a high risk of contracting disease-causing microbes or dangerous chemicals that not only irritate the skin but also can cause breathing problems or allergies. After visual inspection, when you decide which area needs immediate cleaning, shut down the fans and the entire cooling tower system using a tagout procedure to avoid accidental startup. Cleaning a working cooling tower can be risky or even kill the cleaners.
Wear personal protective equipment (PPE), such as:
Safety glasses for eye protection: Protect your eyes from harmful gasses, splashes, and dirt with glasses.
Gloves: To prevent direct contact with perilous chemicals, cleaning agents, and other wild materials. Also, make sure to wear full-sleeve shirts to guard your skin.
Mask: There is evident leakage of dangerous gasses or substances while cleaning and scrubbing the clogging areas of cooling towers. Wear quality respiratory protection, such as a mask, to prevent any unpleasant accident.
Non-Slip Boots: Remember to wear non-slip boots to avoid falls when working on wet surfaces.
Turn of the Cooling Tower and Remove the Debris
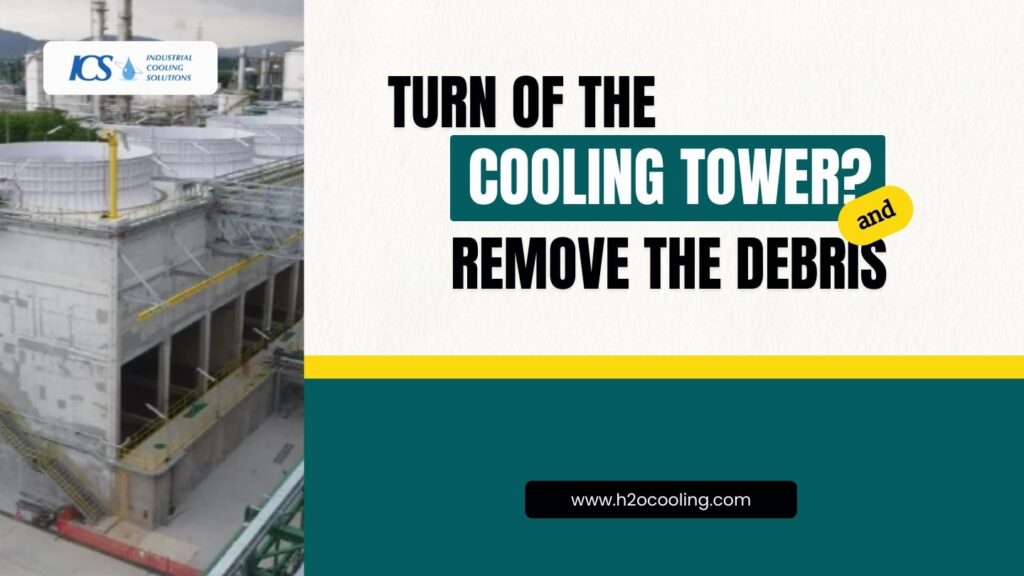
To begin the cleaning, first of all, make sure that the area is clear and notify the relevant personnel. Switch off the fans and pumps and close the inlet and outlet valves. These chillers operate at high voltages, typically ranging from 480V to 13.8kV or even higher, depending upon the size and its application. To ensure the safety while cleaning the cooling tower:
- Shut down the system before maintenance.
- Make sure the zero energy state by using a voltage tester.
- Use electrical isolation devices such as circuit breakers.
- Ground equipment and personnel to prevent electrical shocks.
- Provide regular training sessions which will help prevent accidents, ensure compliance, and maintain a safe working environment.
After carefully de-energizing the system, clear the surrounding area and remove the external screens, louvers, and access panels to cleanse the interior debris and obstructions.
Chemical Disinfection
Choosing the right chemical is critical for the effective disinfection of cooling towers. How to choose the best material for chemical cleaning your cooling towers basically depends on the material of the tower system and the type of contaminants or deposition.
Usually, the combination of chemical disinfectants and cleaning methods is adopted while cleaning cooling towers, for example:
- Acid-based cleaners like phosphonates or bicarbonates are recommended to remove rust, scale, and mineral deposits. These cleaners are rich in phosphoric acid and hydrochloric acid (Hcl), which are helpful in removing rust.
- Different biocides are used to inhibit and kill the growth of microorganisms such as algae or bacteria (present in low-quality water). There are multiple types of biocides available on the market to disinfect cooling towers based on the microorganism types and their immunity. Some common pesticides include chlorine (Cl), chlorine dioxide, hydrogen peroxide, Isothiazolinones, and ammonium compounds.
- When it comes to cleaning sticky oils, biofilms, silt, greases, and organic deposits, alkaline cleaners are a great choice, for example, potassium hydroxide (KoH), sodium hydroxide (NaOH), sodium carbonates, and phosphoric acids.
- Sodium carbonates and their bicarbonates, sulfuric acid, citric acid, or caustic soda, are usually used to adjust the pH of the cooling tower water, and water treatment, and maintain its quality to avert the chances of scaling and corrosion.
- Make sure to follow instructions and guidelines while handling these chemicals. Moreover, it is critical to have experts who choose and use these disinfectant materials for better results.
Clean the Fill Media and Fill Material
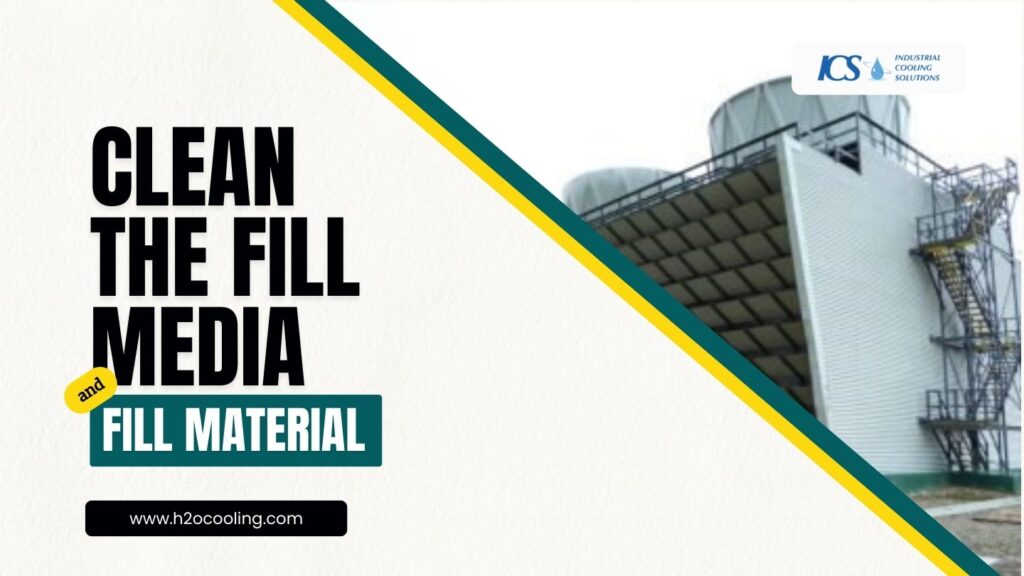
The fill media and material are vital in heat transfer, and any debris or contamination can reduce the tower’s effectiveness. Therefore, regular cleaning of these in a cooling tower is essential to maintain its efficiency and performance. There are many functions of these fill packs and fill sections, such as:
- Provide a larger surface area for heat exchange between water and air.
- Allow for smooth and efficient water circulation throughout the tower.
- They prevent clogging and blockages by trapping debris and sediment and ensure uninterrupted airflow and water flow.
- Inhibit biological growth, such as bacteria and algae, which otherwise hinders the tower’s performance.
To clean it, start by inspecting the fill media and material for damage or wear and remove large debris and sediment. Use a low-pressure water jet or spray nozzle to clean the fill media and apply a cleaning solution or detergent specifically designed for cooling towers.
Steep the fill material for 30-60 minutes, then rinse thoroughly with clean water to remove smut and cleaning solution. Inspect and replace the damaged fill material and then assemble and restart the cooling tower.
Wash the Hot Deck
The hot deck is the uppermost part of the cooling tower system from where the hot industrial water is distributed on the fill media in the form of tiny water droplets. Any blockage in the spray nozzles, fill material, or water distribution pipes can reduce the heat transfer rate, ultimately leading to poor and ineffective cooling.
First of all, clean the hot deck, all the holes, and the spray nozzles to scrub the sediments, mineral deposits, scaling, and corrosion out and out. Washing these areas can successfully prevent the mixing of impurities or debris from the distribution water after complete cleaning and chemical treatment. Use a brush or a medium-pressure washer to remove and clean the surface deposition and contamination from the hot deck.
Be aware of using high-pressure water spray of hard brush, as they can damage the hot deck ultimately. Thoroughly flush the hot deck with lukewarm water to wash off all remaining debris and cleaning agents.
If you observe any clear signs of missing or impairments of spray nozzles, take immediate action tp buy from a reputed cooling tower parts dealer for efficient water distribution and maximum heat exchange.
Missing and damaging spray nozzles are responsible for insufficient heat exchange between warm water and moist air, reducing the overall working capacity of the cooling tower.
Clean the Drift Eliminator and Tower Basin
Drift eliminator removes water droplets from the air stream and prevents drift and water loss which ultimately minimizes the fog or mist formation. The cold cooling tower basin collects and distributes water throughout the tower. These basins also store water for recirculation and regulating water levels. Both are essential components and with regular usage, debris, and biological growth accumulate and require proper cleaning for optimal efficiency of the tower.
To start cleaning these parts of dirty cooling towers:
Remove drift eliminator panels or sections and inspect for dust, biological growth, and any mineral deposits. Use low-pressure water jets or spray nozzles to clean these components. Then, apply a cleaning solution or detergent and rinse thoroughly with water.
Cleanse the drift eliminator and tower basins every 6-12 months or as the manufacturer recommends. Don’t forget to document the cleaning process to schedule the next washing time.
Clean and Lubricate the Cooling Tower Fans
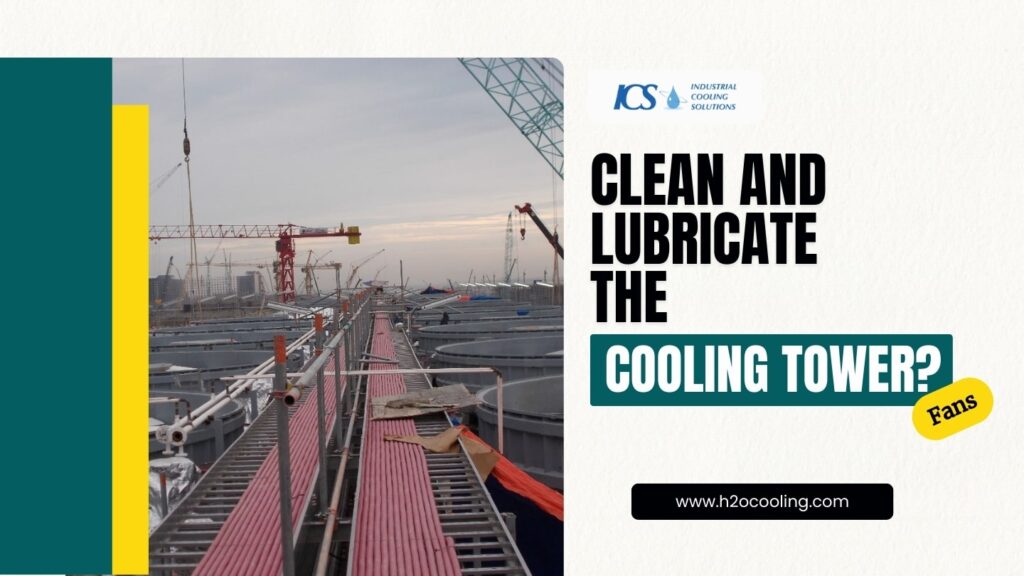
They are one of the critical cooling tower components and need to be fully functional for continuous airflow generation for maximizing the evaporative cooling process and direct contact of air water for optimizing the heat exchange procedures.
Clean and lubricate the cooling tower fans, unlock the access panel to reach the components, remove the debris of corrosion from the fan blades, and clean thoroughly to make them free of dirt and grease.
If fan blades are not perfectly cleaned or free from depositions, you can use a mild detergent to wipe them off and observe keenly for any sign of damage or wear. Check all fan bolts, tighten them, and lubricate the fan parts with a lubrication gun. Your lubricant must be of good quality.
After lubrication, close the cooling tower fan panel and check for any noise or vibration. If there is no unusual noise coming from fans, move toward the next step.
Make documentation and keep all the records of cooling tower maintenance and cleaning. Primarily, the cooling tower works perfectly when cleaned at least twice or thrice a year in addition to regular weekly, monthly, and quarterly inspections and maintenance.
Proper maintenance and a complete cooling tower cleaning process are mandatory to prevent the growth of algae and legionella bacteria. You can also take the cooling tower exerts to schedule the following cleaning and advise to minimize any risk.
Why Work with Cooling Tower Cleaning Experts?
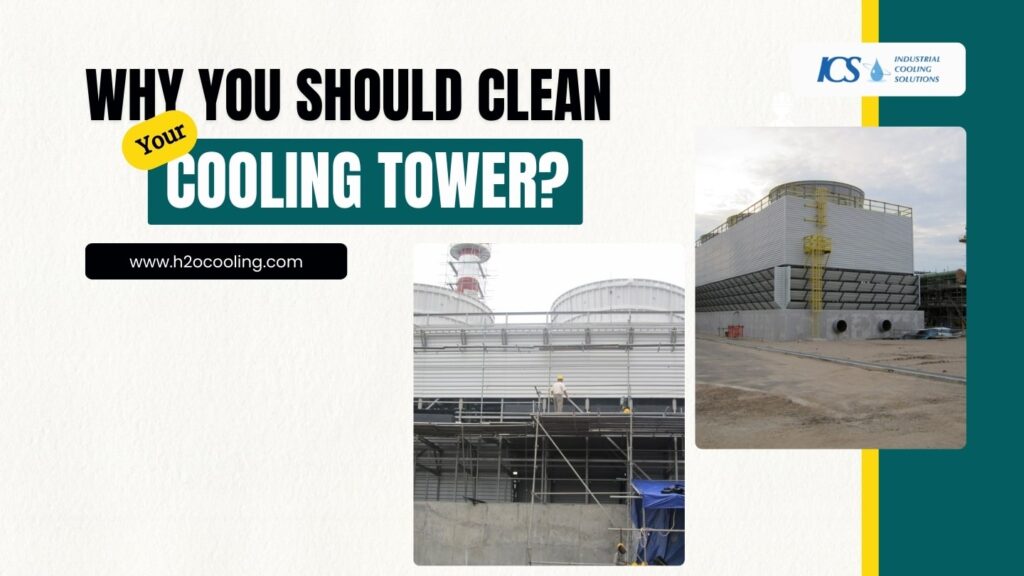
Don’t take risks on the efficiency and performance of your cooling towers. Whether you want to take expert advice on existing cleaning services or want to hire a seasoned professional for complete maintenance, our team is here to help you. We offer comprehensive cleaning and maintenance personalized guidance on cooling tower safety and efficiency.
Our experienced technicians will identify potential issues, rectify problems, and implement proactive measures to prevent future downtime. Our customized solutions address Legionella risk management, corrosion prevention, water quality optimization, and regulatory compliance. Just reach out to book an appointment.
Conclusion
Regular care and cooling tower cleanings are vital for the effective working of cooling towers, as with time, most of its parts and components wear and tear and need proper inspection, repairs, and replacement. In this article, we have discussed the benefits of cooling tower cleaning, the essential steps of cleaning, and why working with cooling tower cleaning experts is preferred in case of any confusion. Therefore, don’t overlook the importance of cleaning the towers and concentrate on working and maintaining cooling towers.